How to Detect and Protect Against Pressure Gauge Failure
How Can You Tell A Gauge Is Broken or May Fail?
Dave Ross, Senior Technical Service Engineer
Pressure gauges seem small but are a critical part of systems across industries. The visual indication of system pressure they provide lets you know whether everything is operating within the desired range or if a problem is imminent. A gauge not functioning accurately may lead to lower quality in your system output due to the loss of valid data and the resulting effects of too much or too little pressure in the system. A gauge that fails can also release system fluid into the environment and result in potential injury to employees, damage to your system requiring downtime and money to repair, and lost system output and profits.
Recognizing the indicators of pending gauge failure and the cause will help you quickly recognize that the pressure readings are no longer accurate, helping you avoid undesirable outcomes.
If you suspect you may not have the best gauge for your application, read on to learn what warning signs of failure look like.
What Are the Signs of Gauge Failure?
The top five pressure gauge failure causes, the signs you will see, and steps you can take to solve the problem, are:
Overpressure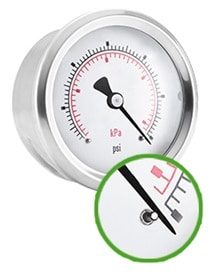
A gauge with its pointer pegged against the stop pin indicates it is operating near or past its maximum pressure. This means the installed gauge has an incorrect pressure range for the application and is incapable of reflecting the system pressure. As a result, the Bourdon tube may rupture and cause complete gauge failure.
A Bourdon tube is a curved, hollow tube, typically made from metal, that is inside the gauge. This tube reacts to the system pressure and will move the connected pointer to display a pressure reading on the gauge dial.
Select a gauge with a range rated to two times the expected system operating pressure to provide for a larger window of measurable pressure or include overpressure protection (i.e., a relief valve) in the system preceding the gauge. In extreme system conditions, use a gauge with an orifice restrictor (0.3 mm) to restrict flow, or consider a diaphragm seal option, rather than a Bourdon tube design, for a more robust solution.
Pressure Spikes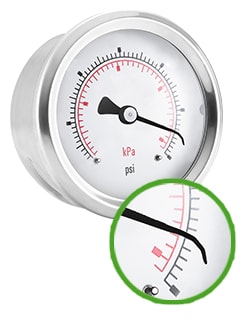
When you see a gauge pointer bent, broken, or nicked, the gauge has likely been subjected to a sudden spike in system pressure caused by a pump cycling on/off or a valve being open/closed upstream. The pointer can be damaged from the force of hitting the stop pin. This abrupt change in pressure can lead to a Bourdon tube rupture and gauge failure.
Evaluate your system design to eliminate unpredictable spikes in pressure and the resulting strain on system components, including the gauge. Another option is to select a gauge with a larger pressure range to accommodate any expected spikes in pressure.
Mechanical Vibration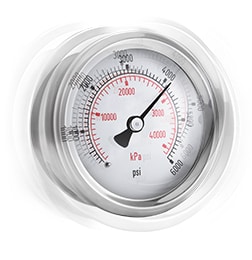
A misaligned pump, reciprocating compressor, or a poorly mounted gauge can result in a missing pointer, window, window ring, or back plate. You may also see black dust on the dial or scrapes on the dial from a loose pointer. The gauge movement connects to the Bourdon tube, and vibration can break the movement component, meaning the dial no longer reflects the system pressure. Using a liquid case fill will dampen the movement and eliminate or reduce the avoidable vibration in the system. In extreme system conditions, use a snubber or a gauge with a diaphragm seal.
Pulsation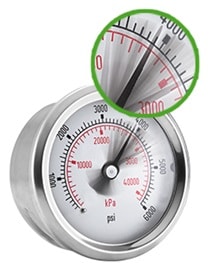
Frequent, fast cycling of fluid through the system creates wear on the gauge movement components. This can affect the ability of the gauge to measure pressure and will be indicated by a fluttering pointer. This condition can lead to a Bourdon tube rupture and complete gauge failure. Redesign your system to reposition the gauge within your application to reduce the cycling speed seen by the gauge and maintain the needed measurement integrity. Should you be unable to redesign your system, using a gauge with liquid fill, a gauge orifice restrictor, or a snubber will help reduce the effects of pulsation.
Excessive Temperature/Overheating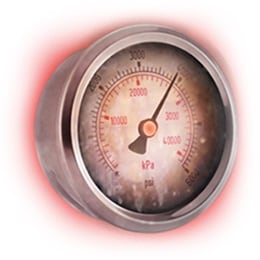
A gauge that is incorrectly mounted or located too close to excessively hot system liquid/gas or components can have a discolored dial or liquid case fill from the breakdown of the gauge components. Elevated temperature stresses the pressure system and affects measurement accuracy by causing a strain on the metal Bourdon tube and other gauge components. Selecting a gauge with a different temperature rating will better accommodate the possible range the system will see. For extreme temperature applications choose a gauge with a diaphragm seal or a diaphragm seal with a cooling element.
The reality is, gauges can fail. Knowing how to detect a pending failure can help you avoid the worst potential consequences but choosing the right gauge for your needs is even more important. Selecting the best gauge for your application is not always easy, but investing the time to analyze the needs of your system and make a better decision upfront will reduce the chance of premature failure paying off in the form of a safe facility, accurate system pressure measurements, and reduced system liquid lost from having the wrong gauge installed.
Interested in evaluating your gauges and system design?
> Download your printable guide to the top five causes of gauge failure.
Related Articles
7 Tips for Building Safer Industrial Fluid Systems
When designing industrial fluid systems, plant safety must always remain top of mind. Learn how your team of engineers and technicians can reduce safety risks and maintain system uptime with essential fluid system building and design tips.
5 Common Process Analyzer System Revelations over 50 Years of Training
Sampling systems can be one of the most challenging systems within your plant to both design and operate. Industry veteran and industrial training instructor, Tony Waters, shares his trainees’ top revelations over the past 50 years.
Field Engineering Q&A: What to Know for Better Fluid and Sampling System Performance
Swagelok Field Engineering Services can help fluid and sampling system operators solve issues from leaks to sampling inaccuracy and everything in between. Here’s everything you need to know about Swagelok Field Engineering.