分析計装システムの時間遅れを理解・測定する
分析計装システムの時間遅れを理解・測定する
サンプリング・システムで時間遅れが生じたために、プロセス分析器で正確な結果が得られないというのはよくある話です。 プロセスの測定は一瞬で終わりますが、分析器の応答はそうはいきません。 取出し口から分析器に到達するまでの間に、常に時間遅れが発生します。 分析計装(AI)システムで時間遅れが発生する可能性がある個所は次の通りです: プロセス・ライン、取出し口とプローブ、フィールド・ステーション、中継ライン、サンプル調整システム、流路切り替えシステム、分析器(下の図をご参照ください)
時間遅れは、累積していくということを頭に入れておきましょう。 時間遅れとは、流体がプロセス・ラインから分析器に到達するまでにかかる 合計時間 です。これには、最終的な分析に必要な時間を含みます。 例えば、ガス・クロマトグラフによるサンプル分析に5分かかるとすると、サンプル調整システムと流路切り替えシステムの時間遅れだけでなく、中継ライン、フィールド・ステーション、取出し口、プローブの時間遅れにもこの5分を追加する必要があります。 さらに、この小計時間を、流体がモニタリング対象のプロセス・ユニットから取出し口へ移動するのにかかる時間に追加しなくてはいけません。 重要なのは、モニタリング対象のプロセス・ユニットから分析器に至るまでの合計時間なのです。
残念ながら、時間遅れが軽視されていたり、無視あるいは誤解されていたりするケースは少なくありません。 分析器の専門家や技術者は、分析に適したサンプルを作り出すことに集中するあまり、時間遅れのことは忘れがちです。 また、分析測定は一瞬で終わると考えている分析器の専門家もいますが、サンプリング・システムが応答時間1分という業界標準を達成できず、時間遅れの可能性が大幅に高まっているケースは珍しくありません。 ただ、サイクル時間が長い場合を含め、時間遅れを常に最小限に抑えることができれば理想的ですが、業界標準を超過することが必ずしも問題になるわけではありません。 その点については、プロセスの状態に基づいて、許容可能な時間遅れをプロセス・エンジニアが判断する必要があります。
問題なのは、時間遅れがシステム設計者の想定を上回った場合です。 時間遅れの予測が甘かったり、前提が誤っていたりすると、プロセス制御ができなくなるおそれもあります。 時間遅れの原因を理解し、遅れを計算する方法や、許容誤差内での遅れを見積もる方法を習得すれば、遅れの短縮はもちろん、システム全体の応答性の向上にもつながります。
プロセス・ライン、取出し口、ファスト・ループ、中継ラインの配置によって効率を最大限に高める
時間遅れを短縮するには、できるだけ分析器の近くに取出し口を設置するというのが一般的な方法です。ただし、これが不可能な場合もあります。 取出し口は、遅延の発生源[ドラム、タンク、たまり部、流れが悪いライン、使用していない装置(本来は、流れ改善のために撤去することが望ましい)など]の一次側に配置しますが、場合によっては前述のさまざまな要因から、プロセス分析器の近くに取出し口を設置することができない場合もあります。 取出し口と分析器の距離が長くなる場合は、流体を高速で分析器に供給可能なファスト・ループを使用することをお勧めします。 適切に設計すれば、ファスト・ループを使用することで、分析器のラインに比べて大幅に流れが速くなります。
圧力を下げることで時間遅れを短縮する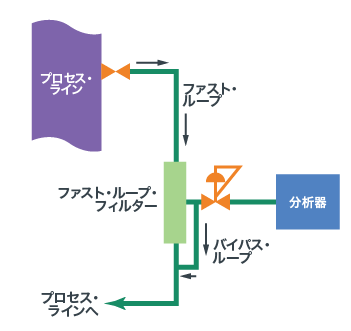
フィールド・ステーションでガスを使用すると、中継ラインまたはファスト・ループの圧力を下げることができます。 流量が同じであれば、中継ラインの時間遅れは、絶対圧力の降下に比例して短くなります。 つまり圧力が半分になると、時間遅れも半分になります。 フィールド・ステーションは、できるだけ取出し口の近くに配置しましょう。 また、圧力降下のスピードが速いほど、時間遅れを短縮することができます。
液体サンプルの場合、流量調節型フィールド・ステーションを使用することはありません。 また、泡が発生しないように、液体は圧力が高い状態を維持することをお勧めします。 液体サンプルをガスとして分析する場合は、フィールド・ステーションで気化レギュレーターを使用することも可能ですが、 これによって大幅な時間遅れが発生することになります。 流体が液体からガスに変化すると、体積が大幅に増えます。 増加の比率は、液体の分子量に応じて変化します。
一般的に、気化レギュレーターに達する前の液体の流量と比較すると、レギュレーターを通過した後の蒸気の流量は300倍以上にも達します。 例えば、蒸気の流量が500 cm3/分の場合、液体の流量は2 cm3/分未満です。つまりこの液体は、長さ10フィートの1/4 インチ・サイズ・チューブを通過するのに25分かかることになります。 この時間を短縮するには、レギュレーターの前に取り付けるチューブの容積を小さくすることが必要です。 例えば、サイズが1/8インチで長さが1フィートという短いチューブを使用すれば、わずか30秒で液体をレギュレーターに到達させることができます。 ただし、この時間にプローブでの時間遅れを追加する必要があります。 プローブの径が小さいほど、応答時間は短くなります。
応答を速めるには、分析器の近くに気化レギュレーターを配置するという方法もあります。 この場合、2つ目の液体ファスト・ループを使用して、ファスト・ループ・フィルターの後にレギュレーターを取り付け、確実に流れが気化レギュレーターに到達するようにしてください。 これで、低速の液体がレギュレーターに供給される量をできる限り抑えることができます。
流路の切り替え
時間遅れをできるだけ抑えるには、流路切り替えアセンブリーで古いサンプル物質を速やかにパージしつつ、新しい流れを分析器に供給する必要があります。 流路切り替えに ダブル・ブロック/ブリード(DBB)バルブ を使用すれば、たまり部を最小限に抑えることができ、バルブからの漏れによる流路間でのコンタミネーション発生を回避することができます。この構成は現在、従来型のコンポーネントのほか、ミニチュア・モジュラー型があります。
従来のDBB構成は、下の図のようなカスケードDBBとなります。 カスケードDBBでは、ティー型ではなく2個目のブロック・バルブを使用してたまり部を排除します。
DBBカスケード構成は、圧力の降下と流れの低速化を招く可能性があるため、使用する場合には流路を考慮する必要があります。 圧力降下の程度は、流体のCv値(流れ抵抗の測定値)から推測することができます。 Cv値が低いほど圧力降下は大きくなり、流れが遅くなります。
DBBカスケード構成ではメイン流路(Stream 1)に大幅な圧力降下は発生しませんが、Stream 2以降では圧力の降下量が大きくなり、流路も長くなります。その結果、二次側への到達時間が長くなります。 つまり流路によって供給時間にばらつきが出るため、すべての流路に同じパージ時間を設定することが難しくなります。
フロー・ループを内蔵したDBB構成(下の図を参照)であれば、DBBカスケード構成の特長をすべて生かしつつ、全流路の圧力降下を一律に最小限に抑えることができます。 これで、各流路のCv値(つまり、各流路の供給時間)は等しくなります。 Cv値が0.3のコンポーネントは、Cv値が0.1のコンポーネントに比べて1/3の圧力降下となります。
サンプル調整システム
サンプル調整システムは、サンプルをフィルタリングし、適切な相を保持し、圧力、流量、温度を調節して、分析に適した状態にします。 この処理を小型のシステムで行う場合は、比較的小さいコンポーネント(圧力計、レギュレーター、面積式流量計、フロー・コントローラー、逆止弁、調節用バルブ、ボール・バルブなど)を数多く使用します。 また、十分なスペースが確保できない場合、ミニチュア・モジュラー型のコンポーネントを使用するケースも多く見られます。 これらの上部取り付けタイプのコンポーネントは、New Sampling/Sensor Initiative(NeSSI)に従い、ANSI/ISA 76.00.02規格に準拠して製造されています。 流路切り替えバルブの場合と同様、ここでも重要なのは内容積よりも圧力降下です。 コンポーネントを選定する際は、製造業者が開示しているCv値を比較してください。
サンプル調整システムで使用されているその他のコンポーネント(フィルター、ノックアウト・ポット、液体除去用フィルターなど)は、流入するサンプルと古いサンプルが混合すると、大幅な時間遅れを生じさせるおそれがあります。 この時間遅れを短縮するには、洗浄が有効です。フィルターやノックアウト・ポットを洗浄することで、古いサンプルの95%を除去することができます。 ただし、洗浄にはコンポーネントの3倍の容積が必要になります。 また下の図のように、出口と入口が隣接していることが前提となります。
入口と出口が上の図のように配置されているフィルターを考えてみましょう。 流速が100 cm3/分、フィルターの容積が100 cm3とすると、古いサンプルの95%を確実に洗い流すのに3分かかります。 つまり、適切なサンプルを得るには、この分析計装システムの時間遅れを算出した結果に3分を追加してください。 プロセス・ラインでさまざまな容積のコンポーネントが混在している場合も、これと同じ式を当てはめることができます。
分析器
一般的にガス・クロマトグラフは、サンプルの分析に5分から10分かかります。 赤外線または紫外線を利用した分析器を使用することで処理時間を大幅に短縮でき、わずか数秒で分析が完了します。 分析器の専門家、技術者、エンジニアの方々は、分析器がサンプルの処理に要する時間を把握しておきましょう。 この時間も、取出し口から分析器に到達するまでに発生する、上記の時間遅れの推定合計値に加えてください。
最後に
今回紹介した方法で合計時間遅れを計算すると、許容誤差範囲を推測することが可能になります。 モニタリング対象のプロセスから分析器に到達する間に発生する合計時間を算出し、この遅れに関わっているすべてのコンポーネントを合計時間に追加してください。 時間遅れは、分析器の専門家による対処が必要な問題です。 特にトラブルが発生しやすい部分(フィールド・ステーションのプローブや気化レギュレーターなど)でサンプルの処理時間の推測を誤ると、分析器の専門家の努力が水の泡になるばかりか、分析器の存在意義が失われることにもなりかねません。 分析器の専門家は、 流体システムのプロバイダー やコンサルタントの協力を得ながら、コンポーネントと構成(取出し口の場所、ファスト・ループのセットアップ、適切なチューブ径、経路切り替えの構成など)を的確に選択し、時間遅れの改善に努めてください。
関連コラム
レギュレーターを使用して分析計装システムにおける時間遅れを短縮する方法
分析システムでは、時間遅れが軽視されていたり、誤解されていたりするケースは少なくありません。 この時間遅れは、レギュレーターでコントロールすることができます。 今回は、分析計装システムにおける時間遅れを小さくする方法を紹介します。
サンプリング・システムの時間遅れ: 4つのチェック・ポイント
プロセス分析器サンプリング・システムでは、測定値を取得するまでに必ず時間の遅れが発生します。 この時間遅れを軽視すると、プロセスの制御に悪影響が及ぶことがあります。 今回は、時間遅れを短縮するための4つのポイントを紹介します。
サンプリング・システム:プロセス分析器の精度にまつわる8つの課題
サンプリング・システムの専門家であり、一般産業向けトレーニング講師としても長い経験を持つTony Waters氏が、プロセス分析器の精度にまつわる8つの課題を特定・解決する方法を、自らの経験に基づき紹介します。特にプラント・マネージャーや設計エンジニアの方は是非ご一読ください。